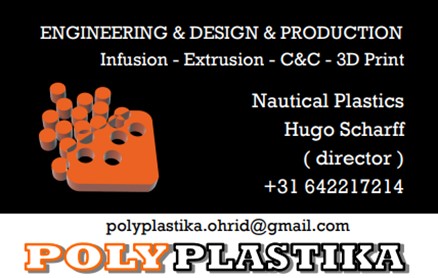
A partner with experience
Built on a partner with experience in the field of manufactored products made in North Macedonoia.
Polyplastika is a young and dynamic company that has its origins in the yachting industry. Polyplastika trades, designs and produces plastic parts which are intended for watersports and outdoor activities. We have the ability and knowledge to convert the customer’s idea into an exclusive product. In addition, we also have a range of standard products which we can often supply from stock.
The production takes place in North Macedonia, an excellent and traditional plastic production country. Here we have Hot Molding machines, extrusion machines, C&C cutters and 3D printers, all based on obtaining the best quality. The most commonly used plastics include: ABS, PA6 optionally reinforced fiberglass and PVC. Because we make the molds and tools in-house, we can respond directly to the customer demand. Our customers are suppliers for yacht building and nautical shops, but also shops for outdoor activities. We mainly focus on the European market, simply because we know it best.
If you have any questions about the professional field, we will be happy to help you and we may be able to help each other. Please do not hesitate to contact us, we will be happy to get in touch with you to discuss a new product, for a quotation or sales cooperation.
Hugo Scharff Polyplastika
Injection moulding
Injection moulding is a manufacturing process that allows for parts to be produced in large volumes. It works by injecting molten materials into a mould (or ‘mold’ in the United States). It is typically used as a mass production process to manufacture thousands of identical items. Injection moulding materials include metals, glasses, elastomers and confections, although it is most commonly used with thermoplastic and thermosetting polymers.
How does it Work?
The first stage of injection moulding is to create the mould itself. Most moulds are made from metal, usually aluminium or steel, and precision machined to match the features of the product they are to produce.
Once the mould has been created by the mould-maker, the material for the part is fed into a heated barrel and mixed using a helical shaped screw. Heating bands melt the material in the barrel and the molten metal or molten plastic material is then fed into the mould cavity where it cools and hardens, matching the shape of the mould. The cooling time can be reduced through the use of cooling lines that circulate water or oil from an external temperature controller. Mould tools are mounted on plate moulds (or ‘platens’), which open once the material has solidified so that ejector pins can eject the part from the mould.
Extrusion moulding extrudes, or forces out, materials through a die to create such products as hoses, drinking straws, rods, pipes profiles. A die is a manufacturing tool used to shape or cut material via a press, or machine that uses pressure to compact or otherwise reshape an object.
Process
Extrusion moulding is done via an extrusion machine. The machine motor turns a screw, which feeds plastic through a heater. The granules in the plastic melt into liquid, which is pushed through the die tool. This forces the material into a tube shape determined based on the specific shape of the die. The material forms a solid tube shape after cooling.
Extrusion moulding
CNC Milling
CNC milling technology revolves around the manufacture of holes, slots and openings in all kinds of materials. It is a form of machining that involves working with a milling cutter. For that milling you use a machine in which a rotating milling cutter does the work. Unlike a drill, the cutter does not move down towards the tip, but sideways. As a result, in the metal industry you can process steel or other materials in such a way that holes, slots and recesses are created. Which material is milled differs per sector: in aircraft construction you are more likely to use a milling cutter for aluminum, but milling cutters have also been designed for materials such as Plastics
Three-dimensional (3D) printing is an additive manufacturing process that creates a physical object from a digital design. The process works by laying down thin layers of material in the form of liquid or powdered plastic, metal or cement and then fusing the layers together.